When it comes to aggregate batching in asphalt plants, choosing between multi-bin and single-bin machines is a critical decision that impacts both gradation adjustment flexibility and equipment footprint. Each type has its advantages and drawbacks, and understanding these differences is essential for optimizing operations.
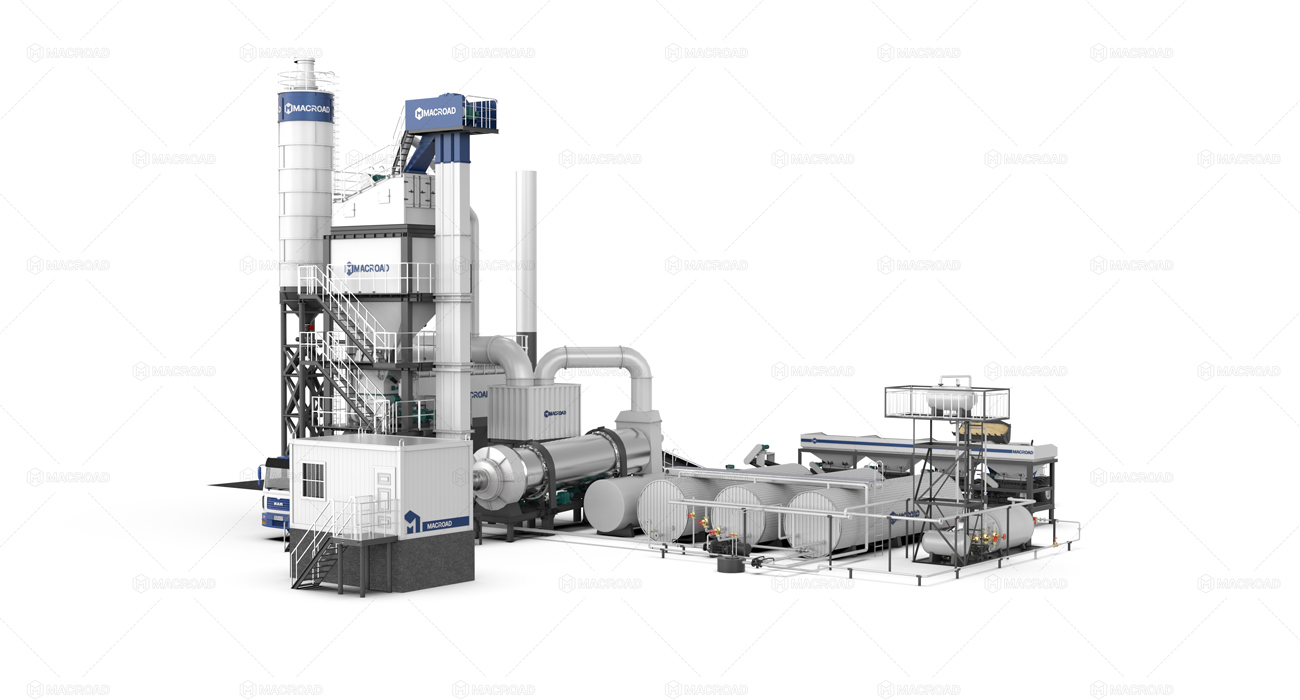
Gradation Adjustment Flexibility
One of the most significant factors in asphalt production is the ability to adjust the gradation of aggregates accurately. Multi-bin aggregate batching machines offer superior flexibility in this regard. These machines can store multiple types of aggregates in separate bins, allowing operators to mix different materials in precise proportions. This capability is particularly beneficial for projects requiring specific gradation profiles to meet performance specifications.
For example, in a stationary asphalt plant, a multi-bin system can easily accommodate various aggregate sizes, ensuring that each batch meets the necessary quality standards. This flexibility is especially valuable when dealing with varying local aggregate supplies, as it allows for quick adjustments based on availability and project requirements. In contrast, single-bin machines are limited to one type of aggregate at a time, which can hinder the ability to achieve the desired mix and may lead to inconsistencies, particularly in projects with strict gradation requirements.
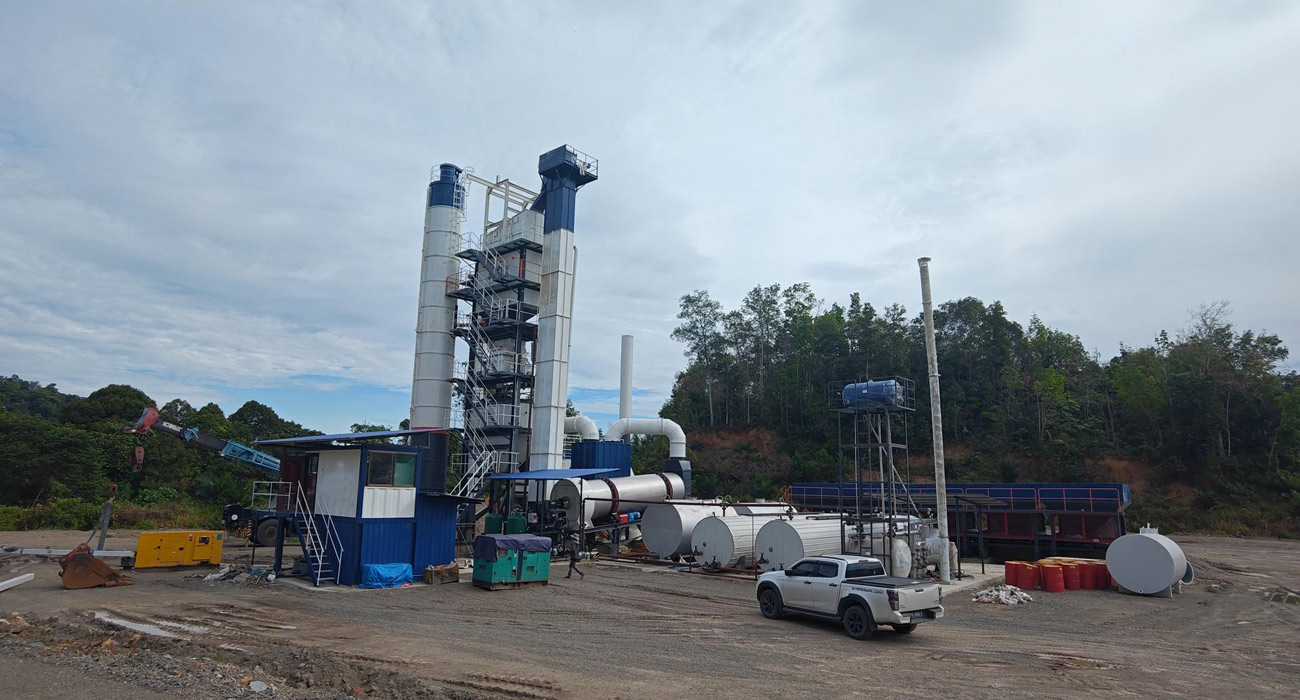
Equipment Footprint Considerations
While multi-bin machines excel in gradation adjustment, they typically require a larger physical footprint compared to single-bin systems. The increased number of bins necessitates more space for installation, which can be a significant consideration for asphalt plants with limited operational areas. This is especially relevant in urban settings, where space is at a premium and operational efficiency is crucial.
Single-bin aggregate batching machines, on the other hand, occupy less space, making them an attractive option for asphalt plant mobile or smaller fixed operations. Their compact design allows for easier integration into existing facilities, enabling operators to maximize production capabilities without the need for extensive modifications to the plant layout.
Despite their space-saving advantages, single-bin systems may require more frequent adjustments and additional handling of materials to achieve the desired gradation, which can affect overall efficiency. This trade-off between footprint and flexibility should be carefully considered based on the specific needs of the operation.
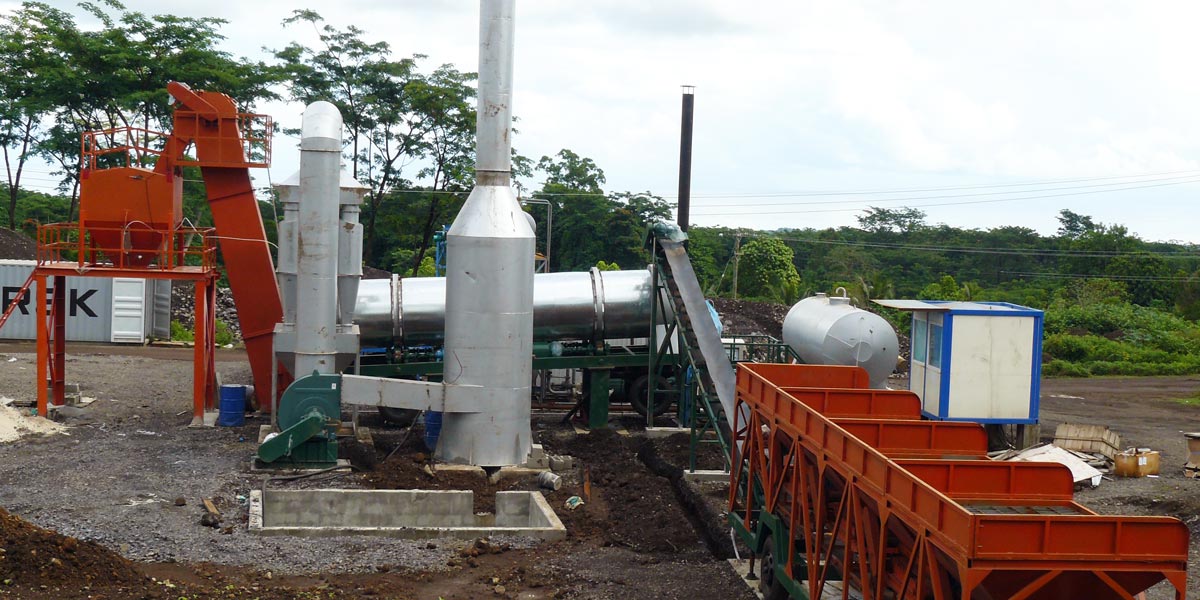
Balancing Flexibility and Space
Ultimately, the choice between multi-bin and single-bin aggregate batching machines depends on the specific requirements of the asphalt manufacturing plant and the projects it undertakes. If a plant frequently deals with diverse aggregate specifications and needs to respond quickly to changing demands, a multi-bin system may be the best investment. The added flexibility can lead to improved product quality and customer satisfaction.
Conversely, if space is a constraint and the plant primarily operates with a limited variety of aggregates, a single-bin system may be more practical. The smaller footprint can facilitate easier installation and operation, while still meeting the basic needs of the production process.
In conclusion, both multi-bin and single-bin aggregate batching machines have their unique advantages and challenges. By weighing the importance of gradation adjustment flexibility against equipment footprint, asphalt plant operators can make informed decisions that align with their operational goals. Understanding these factors ensures that the selected batching system will enhance efficiency and product quality, ultimately contributing to the success of their asphalt production efforts.