Coconuts are one of the most abundant natural resources on the planet and an important source raw material for the cosmetics, food and energy industries around the world. One important use for coconuts that is in widespread use across the globe is coconut shell charcoal machine (máquina de carbón de cáscara de coco).
This type of fuel is valued for its sweet aromatic smoke. But it is also a top-quality fuel that can be readily made with the simplest and time-tested techniques. It has applications in the field of metallurgy and gold refining as well. Coconut shell charcoal can be ground into a fine granular activated carbon that has many uses from mercury removal to municipal water treatment.
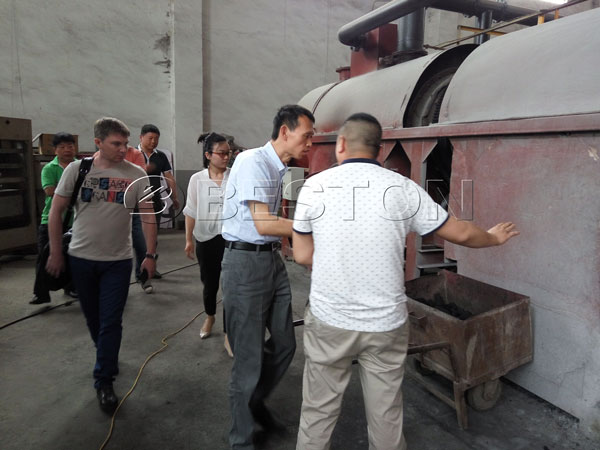
While there are many different ways coconut shells can be transformed into charcoal, this following article will show how to make an efficient coconut shell charcoal manufacturing equipment South Africa that is in use across the world today. Related reading: ¿Cómo hacer carbón vegetal con cáscara de coco?
A Simple Coconut Shell Charcoal Manufacturing Plant
This simple charcoal kiln is made in an extra-large metal drum that has been divided into three operating “sections” each with six ? inch holes drilled in the sides. These holes must be closed and opened to control air passage. The drum must also have a lid fitted with a chimney. The best coconut shell charcoal is produced with limited air intake allowing the coconut to carbonize as opposed to burn.
Begin with a good supply raw coconut shells at the base of the drum leave a small circle in the center and start a fire here with one of the coconut shells. A drop or two of kerosene is the common starter throughout Southeast Asia where this type of production is common. Once the fire begins to catch on you can pile some more raw material on top of the fire till the drum is full.
Once the flames begin to rise again, limit the air intake by covering the drum with the lid and chimney and closing all the holes in the middle and upper sections of the drum. As the shells slowly transform to charcoal they will shrink and fall deeper into the drum. As this happens you will sporadically lift the lid and add more biomass materials to keep the drum full and maximize production.
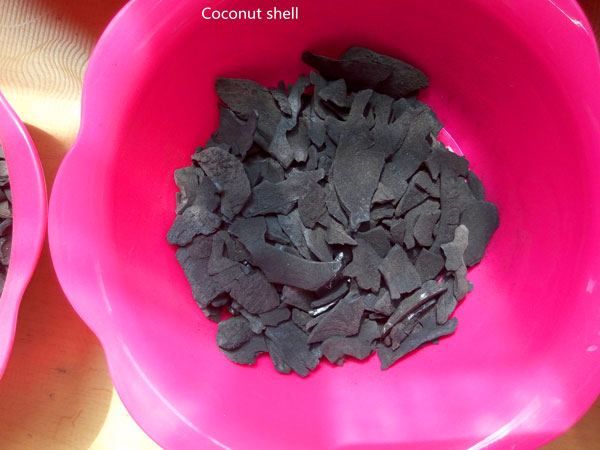
The carbonization will start deep in the drum and you will see a tell-tale warm glow from the air intake holes around the bottom once the raw materials in this section have been successfully converted. Now close all the holes around the bottom of the drum and open all those the middle and upper sections.
Once the same glow shines from the middle section you can close the holes in the middle section and open all the vents in the bottom section. Once the top section has been properly completed, you can close all the holes in the kiln and leave the product to cool off for packaging 8 hours later. Click for the equipo para fabricar carbón.
View more info from about Beston simple charcoal kiln here.